塑料如何着色,有哪些着色方法?
当人们惊叹于塑料的红、黄、蓝、绿时,会不会好奇塑料为什么有这么多颜色?众所周知,塑料基本分为透明颗粒和不透明颗粒,一般呈现乳白色和蜡色,彩色塑料通常是通过着色工艺将着色剂充分渗透到塑料中制成的。塑料着色问题只需记住三点:着色剂、配色、着色工艺。当光作用于塑料制品时,一部分光从制品表面反射产生光泽,另一部分光通过折射和透射进入塑料内部。当它遇到颜料颗粒时,再次反射、折射、透射,显示的颜色就是颜料颗粒反射的颜色。塑料着色是指将一定量的颜料与天然塑料均匀混合分散,使其均匀分散在塑料中,使整个塑料得到均匀颜色的过程。塑料着色常用的方法有色粉加入树脂法、色浆着色法和色母粒着色法。伟创新材,为大家具体简单一下。
一、着色剂
着色剂一般分为三类型,即:有机颜料、无机颜料和溶剂染料。有机颜料是塑料制品中常用的着色剂,由于其着色性能优异、色泽鲜艳、色谱完整、添加量少等特点,被广泛应用于PE、PP等结晶树脂中,但有机颜料价格相当高,通常选择机械加热混合分散法作为工艺。与有机颜料相比,无机颜料耐热、耐光、耐气候性能优异,但颜色不鲜艳,着色能力低,色谱不完整,部分品种毒性较,。目前应用最广泛的无机颜料有二氧化钛、氧化铁红、炭黑等,常用于PA、PBT、PC、POM等灰度树脂中。溶剂染料一般溶于水和油,是一个油性体系,它的耐热性和耐光性较差,但颜色鲜艳透明,因此常用于聚酯透明塑料中。
二、配色
在着色过程中,颜色如何搭配也是重点。配色其实就是根据红、绿、蓝三种基本颜色来匹配想要的颜色,给产品配色还能赋予产品其他功能,如耐候性、耐光性、耐电性、导电性等。颜色的形成主要基于黄、绿、蓝的比例,目前的色系基本是彩色光谱,配色只需根据比色光谱或计算机程序配色即可,而在我司采购颜料,上海精颜化工为您提供免费配色技术。
三、着色工艺
着色工艺一般分为三种,即:色粉加入树脂法,色粉混合树脂法及色母粒法。色母粒法所得产品一般着色力强,便于运输和储存。在后处理过程中,也可适当减少色母粒的加入,因此成本相对较低。如果想赋予产品更多功能,还可以加入其他添加剂,如光稳剂、抗静电剂等。下面伟创新材来为大家具体介绍这三种着色工艺。
1、色粉加入树脂法
色粉加入树脂法又称干混着色、粉末着色、纯颜料着色,可生产普通塑料制品。它简化了生产工艺,直接通过注塑、挤出等加工方式生产使产品着色,避免了树脂因造粒加热而降解。干混着色一般采用白油、松节油等表面活性剂作为分散剂,使着色剂很好地粘附在树脂颗粒上。这种方法适用于颜色量多,产量少的产品。珠光颜料经常使用这种着色方法,减少了混合造粒工序,避免了过度混合的颜料晶片破坏的,不影响塑料制品的闪光着色效果。其次当使用分散性差异很大的颜料时,塑料加工厂难以进行配色时,可以使用颜料供应商提供的粉状配色颜料混合物,即将颜料通过研磨机混合粉碎,在配料中加入一些分散剂或润滑剂,得到易分散的颜料混合物。
干混着色法具有分散性好、成本低、可根据需要任意指定数量、配制方便等优点,节省了色母、色浆等着色剂加工的人力物力消耗,因此成本低,买卖双方不受数量限制,但干混法的缺点是在混合和投料过程中会产生粉尘,污染环境影响工人的健康,且变色时成型设备清洗工作量大,操作麻烦。干混着色要注意混合条件,如混合设备、树脂用量等,特别是时间不同时,其分散状态会发生变化。
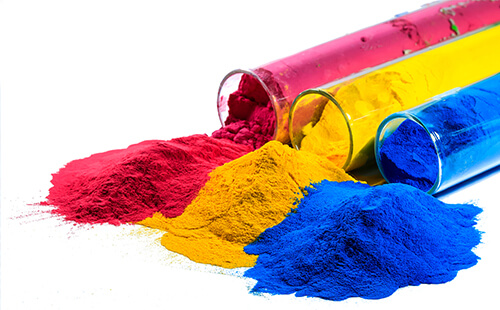
2、着色色粉混合树脂法(色浆)
着色色粉混合树脂法又被称为糊状着色剂或色浆,是利用三辊研磨机、捏合机等混合、混合设备,利用增塑剂、多元醇、脂肪酸甘油酯等液态色彩载体,将颜料研磨成糊状的颜料糊状物。因此,颜料细腻,分散效果好,生产过程中不会发生颜料颗粒的聚集。该着色剂的颜料颗粒厚度小于薄膜的颜料颗粒厚度,可用于生产塑料薄膜着色。当然,由于液体载体的存在,着色过程中没有粉尘污染。
与前两种着色剂相比,糊状着色法由于研磨设备和生产工艺的需要,不像干法那样简单,成本略高,但比母粒成本低1/3,糊状着色法主要用于PVC、不饱和聚酯、聚氨酯等塑料的着色。糊状着色法(色浆)着色的优点是分散效果好,不会形成粉尘污染,缺点是着色剂用量不易计算,成本较高。
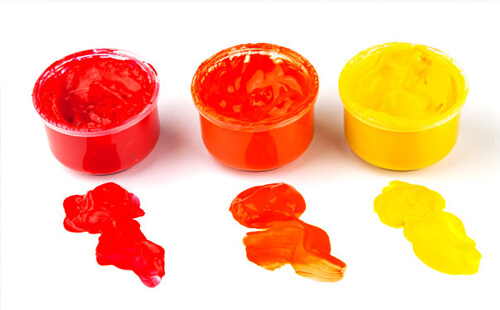
3、色母粒着色法
在配制色母粒时,通常先配制出颜色合格的颜料,然后将颜料按配方配比混入色母粒载体中,最后通过造粒机的加热、塑化、搅拌、剪切,使颜料的分子与载体树脂的分子充分结合,再制成与树脂颗粒大小相近的颗粒,再通过成型设备用于制造塑料制品。使用时只需在着色树脂中加入少量(1%~4%)即可达到着色的目的。不同的塑料制品对色母粒的要求不同,可以根据色母粒的性能指标,如色差、白度、黄度、黄化程度、热稳定性、氧指数、熔体流动速率等进行添加,当然,其工艺颜料还要根据其与色母粒的合成效果,如颜料的细度、流动性、耐化学性、毒性等进行精挑细选。
与色粉加入树脂法相比,色母粒着色具有显著优点:可改善色粉飞扬对环境的污染,使用过程中易变色,无需专门清洗挤出机料斗,配方稳定性强,可保证同一品牌两批次母粒前后的相对稳定性。母粒着色的缺点是着色成本高,配制数量不灵活。此外,将珠光色粉、荧光粉、夜光粉等色粉制成色母后用于塑料着色,比直接与塑料混合效果(如光泽等)降低10%左右,注塑制品更容易产生流线型条纹和接缝。
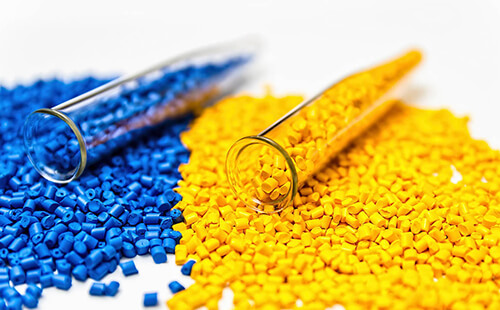